|
 |
|
|
|
Taking Action to Protect Against Silica
|
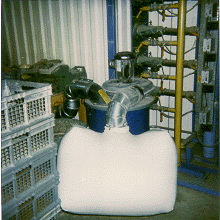 |
Now that I know there is a hazard of silica at my work, what do I do?
|
You must implement the best possible permanent solution to reducing or eliminating the hazard. If such a solution cannot be enacted immediately, then you are required to implement a temporary control to protect your workers until the permanent solution is put in place. |
The following solutions are listed in order of
preference. (Depending on the work site a higher choice may
actually be less effective.):
Note
that all of these options may serve as a permanent solution if necessary. Yet the
ones toward the bottom serve well as temporary controls and the ones toward the top serve
best as permanent controls.
OSHA's
On-Site Consultation Services can provide a more thorough evaluation of your situation and help you decide which measures are best.
Remember: |
All workers breathing crystalline silica dust should have a medical examination that includes:
- Chest X-ray (classified according to the 1980 International Labour Office).
- Classification of Radiographs of Pneumoconioses.
- Pulmonary function test.
- Annual evaluation for TB (tuberculosis).
|
The most sure way to eliminate the silica hazard is to eliminate the silica!
This is especially important for sandblasters, where the abrasive blasting is often done outside
and in different locations, making it impossible to install an engineering control.
The most severe silica exposures occur in abrasive blasting. See the article Stop Silicosis in Sandblasters.
|
Eliminating the silica means
using a different, safer material in place of the silica-containing substance. It is
true that in some cases it is not possible to use a substitute in place of silica, but for
many operations, such as abrasive blasting, there are many possible substitutes, including
those below. |
Alumaglass
Aluminum Oxide
Aluminum Shot
Ambient Polycarbonate
Armex
Apricot Pits
Corn Cobs
Cryogenic Polycarbonate
Emery |
Garnet
Glass Beads
Melamine Plastic
Novaculite
PC+
Polycarbonate
Silicon Carbide
Stainless Cast Shot
Stainless Cut Wire |
Starblast
XL
Steel Grit
Steel Shot
Urea Plastic
Visigrit
Walnut Shells
Wheat Grain
White Aluminum Oxide
Zircon |
Advantages |
Disadvantages |
- Complete elimination of any health hazard related to silica
- Eliminates the need to implement or maintain engineering controls
- These substances are not as dense as silica products which makes them easier to
transport
- They can be moved from job site to job site
|
- May be slightly more expensive than silica products*
- These substances are generally not as hard as silica products which may mean more is
needed to do the job
|
*Using a substitute can still
be cheaper in the long run when you add the cost of engineering controls or protective
equipment needed to combat the silica hazard. Check out the cost-comparison example and the NIOSH study. |
Engineering Controls
Keep silica out of the air |
If silica products must be
used, OSHA requires engineering controls to be used wherever possible. This type of
control involves a mechanical process to eliminate exposure to silica dust. Some of
these controls may be very simple, as can be seen in the examples below: |
- Install a water hose to wet down the dust at the point of generation
- Install local exhaust ventilation
- During rock drilling, flow water through the drill stem
|
- Install dust collection systems onto machines or equipment that generates dust
- Use concrete/masonry saws that provide water to the blade
|
Advantages |
Disadvantages |
- If working properly will eliminate the potential hazard
- Must be installed only once
- Requires little training of workers
- Places no physical burden on workers
|
- Can be expensive to implement
- Requires routine maintenance
|
Work Practices
What employees can do to reduce silica intake |
If workers know about silica
and understand the severity of its health hazard, they will be more likely to do the
following: |
- Know which work operations can lead to silica exposure
- Participate in any air monitoring or training programs offered by the employer
- If possible, change into disposable or washable work clothes at the worksite; shower
(where available) and change into clean clothing before leaving the worksite.
- Do not eat, drink, use tobacco, products, or apply cosmetics in areas where there is
dust containing crystalline silica.
|
- Wash your hands and face before eating, drinking, smoking, or applying cosmetics outside
of the exposure area.
- If using respirators, do not alter the respirator in any way.
- Use type CE positive pressure abrasive blasting respirators for sandblasting
- For other operations where respirators may be required, use a respirator approved for
protection against crystalline silica-containing dust.
- If using tight-fitting respirators do not grow beards or mustaches
|
Advantages |
Disadvantages |
- They can reduce the chance for exposure.
- They may be cheaper in the short run.
|
- They require training of all new employees.
- They require employees to use the practices appropriately.
- They require monitoring of employees at workers.
|
Personal Protective Equipment
A good option as a temporary control. The last choice as a permanent control. |
Personal protective equipment
against silica includes respirators and masks. Respirators should be used only when
the dust controls cannot keep dust levels below the NIOSH Recommended Exposure Level.
There
are many types of respirators, from air-purifying to air-supplying and from a nose
and mouth covering to a full body respirator. You can receive guidance on selecting
a respirator from:
|
Advantages |
Disadvantages |
- They can reduce the chance for exposure.
- They may be cheaper in the short run.
- Useful as a temporary control while the long term solution is being implemented.
|
- They require training of all new employees.
- They require employees to use the equipment appropriately.
- They require setting up a formal PPE program to validate their proper use.
- They require monitoring of all the PPE to insure proper maintenance.
- They can be a health hazard by themselves.
|
|
|
|
|