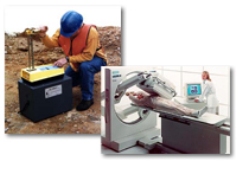
Uranium Enrichment
The uranium enriched in uranium-235 (U235) is required in commercial light-water reactors to produce a controlled nuclear reaction. Several different processes may be used to enrich uranium, as described on this page:
For additional information, see the Related Information (below) or the Fact Sheet on Uranium Enrichment.
Enriching Uranium
Enriching uranium increases the proportion of uranium atoms that can be "split" by fission to release energy (usually in the form of heat) that can be used to produce electricity. Not all uranium atoms are the same. When uranium is mined, it consists of about 99.3% uranium-238 or U-238 (U238), 0.7% uranium-235 or U-235 (U235), and < 0.01% uranium-234 or U-234 (U234). These are the different isotopes of uranium, which means that while they all contain 92 protons in the atom’s center, or nucleus (which is what makes it uranium), the U238 atoms contain 146 neutrons, the U235 atoms contain 143 neutrons, and the U234 atoms contain only 142 neutrons. (The total number of protons plus neutrons gives the atomic mass of each isotope — that is, 238, 235, or 234, respectively.)
The fuel for nuclear reactors has to have a higher concentration of U235 than exists in natural uranium ore. This is because U235 is "fissionable," meaning that it starts a nuclear reaction and keeps it going. Normally, the amount of the U235 isotope is enriched from 0.7% of the uranium mass to about 5%, as illustrated in this diagram of the enrichment process.
Gaseous diffusion is the only process currently being used in the United States to commercially enrich uranium. Gas centrifuges and laser separation can also be used to enrich uranium, as described below.
Gaseous Diffusion
![]() |
The gaseous diffusion process uses molecular diffusion to separate a gas from a two-gas mixture. The isotopic separation is accomplished by diffusing uranium [which has been combined with fluorine to form uranium hexafluoride (UF6) gas] through a porous membrane (barrier), and using the different molecular velocities of the two isotopes to achieve separation. |
Process: In the gaseous diffusion enrichment plant, uranium hexafluoride (UF6) gas is slowly fed into the plant’s pipelines where it is pumped through special filters called barriers or porous membranes. The holes in the barriers are so small that there is barely enough room for the UF6 gas molecules to pass through. The isotope enrichment occurs when the lighter UF6 gas molecules (with the U234 and U235 atoms) tend to diffuse faster through the barriers than the heavier UF6 gas molecules containing U238. One barrier isn’t enough, though. It takes many hundreds of barriers, one after the other, before the UF6 gas contains enough U235 to be used in reactors. At the end of the process, the enriched UF6 gas is withdrawn from the pipelines and condensed back into a liquid that is poured into containers. The UF6 is then allowed to cool and solidify before it is transported to fuel fabrication facilities where it is turned into fuel assemblies for nuclear power plants. The diagram to the right illustrates this gaseous diffusion enrichment process.
Hazards: The primary hazard in gaseous diffusion plants include the chemical and radiological hazard of a UF6 release and the potential for mishandling the enriched uranium, which could create a criticality accident (inadvertent nuclear chain reaction).
Plants: The only gaseous diffusion plant in operation in the United States is in Paducah, Kentucky. A similar plant is located near in Piketon, Ohio, but it was shut down in March 2001. Both plants are leased to the United States Enrichment Corporation (USEC) from the U.S. Department of Energy and have been regulated by the NRC since March 4, 1997.
![]() |
The gas centrifuge process uses a large number of rotating cylinders in series and parallel configurations. Gas is introduced and rotated at high speed, concentrating the component of higher molecular weight toward the outer wall of the cylinder and the lower molecular weight component toward the center. The enriched and the depleted gases are removed by scoops. |
Gas Centrifuge
The gas centrifuge uranium enrichment process uses a large number of rotating cylinders in series and parallel formations. Centrifuge machines are interconnected to form trains and cascades. In this process, UF6 gas is placed in a cylinder and rotated at a high speed. This rotation creates a strong centrifugal force so that the heavier gas molecules (containing U238) move toward the outside of the cylinder and the lighter gas molecules (containing U235) collect closer to the center. The stream that is slightly enriched in U235 is withdrawn and fed into the next higher stage, while the slightly depleted stream is recycled back into the next lower stage. Significantly more U235 enrichment can be obtained from a single-unit gas centrifuge than from a single-unit gaseous diffusion stage. The diagram to the right illustrates this gas centrifuge enrichment process.
One gas centrifuge commercial production plant, the URENCO USA facility owned by Louisiana Energy Services (LES), is currently operating in Eunice, NM. A license was issued to AREVA Enrichment Services, LLC in October 2011 to construct and operate the Eagle Rock Enrichment Facility, a gas centrifuge commercial facility, in Bonneville County, ID. The construction of the facility is currently on hold. USEC Inc., in Piketown, OH, was issued a license in April 2007 to construct and operate the American Centrifuge Plant (ACP). Construction of the ACP began in 2007 but was placed on hold in 2009. In addition, USEC Inc. was granted a license in February 2004 for a demonstration and test gas centrifuge plant, the Lead Cascade facility, that is in operation.
Laser Separation
Isotopic separation of uranium can be achieved based on photoexcitation principles (exciting the molecules using laser light). Such technologies have been named Atomic Vapor Laser Isotope Separation (AVLIS), Molecular Laser Isotope Separation (MLIS), and Separation of Isotopes by Laser Excitation (SILEX). In general, the enrichment process entails using three major systems, which are the laser systems, optical systems, and separation module system. Tunable lasers can be developed to deliver a highly monochromatic radiation (light of a single-color). The radiation from these lasers can photoionize a specific isotopic species while not affecting other isotopic species. The affected species is then physically or chemically changed, which enables the material to be separated. AVLIS used a uranium-iron (U-Fe) metal alloy as its feed material, while SILEX and MLIS use UF6 as its feed material.
No laser separation uranium enrichment plants are currently operating in the United States. However, in July 2007, General Electric - Hitachi submitted a license amendment request to the NRC, seeking approval for research and development associated with laser enrichment to be conducted at its Global Nuclear Fuels-Americas, LLC, facility in Wilmington, NC. The NRC approved the amendment on May 12, 2008, and GE-Hitachi is currently constructing the test loop with the intention of beginning operations in the near future. In addition, in June 2009, GE-Hitachi submitted a license application to construct a commercial laser enrichment plant in Wilmington, NC. The NRC staff is currently reviewing that application.